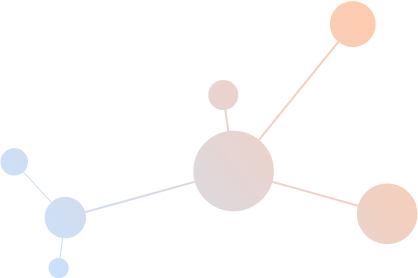
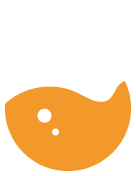
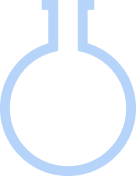
Intro & Solutions
Pulp is the primary requirement of paper production. The regulatory environment is getting stricter in terms of the usage of resources and emission/effluent from mills. The industry has been taking leads in reducing water consumption, improving yield and overall reducing carbon footprint and harmful chemicals to meet regulatory environment and improve profitability.
Modern technologies are helping the industry achieve these higher consumption and emissions standards.
Our chemical offering comprises a wide range of process chemicals to help improve the efficiency of our customer's operations.
We provide innovative and complete solutions for productivity, quality improvement and cost reductions. Various applications in pulp mill range from digester Additives (for white liquor reduction, extractive reduction and dirt/ pitch control), Pitch control chemicals (in digester, BSW, ODL, bleaching and pulp dryers), defoamers (wash aids in the pulp mill, pulp dryers and effluent treatment plant), scale control (pulp mill, bleaching and recovery sections), slag control (recovery boiler), metal ion control (chemical, mechanical and dissolving pulp), enzymes (reduction of bleaching chemicals), Xanthation aids( dissolving pulp and viscose), cleaners (online cleaners and offline cleaners across the pulp mill process), settling aids (recovery section and ETP), conditioners (pulp mill and dryers) to black liquor Viscosity modifiers.
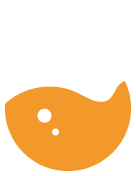
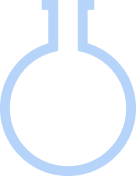
Sub-Segments
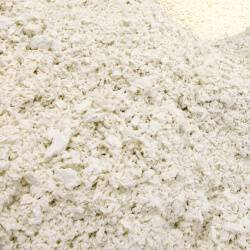
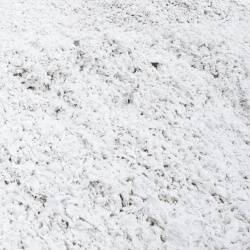
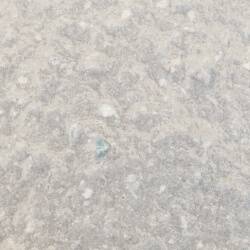
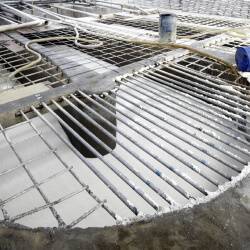
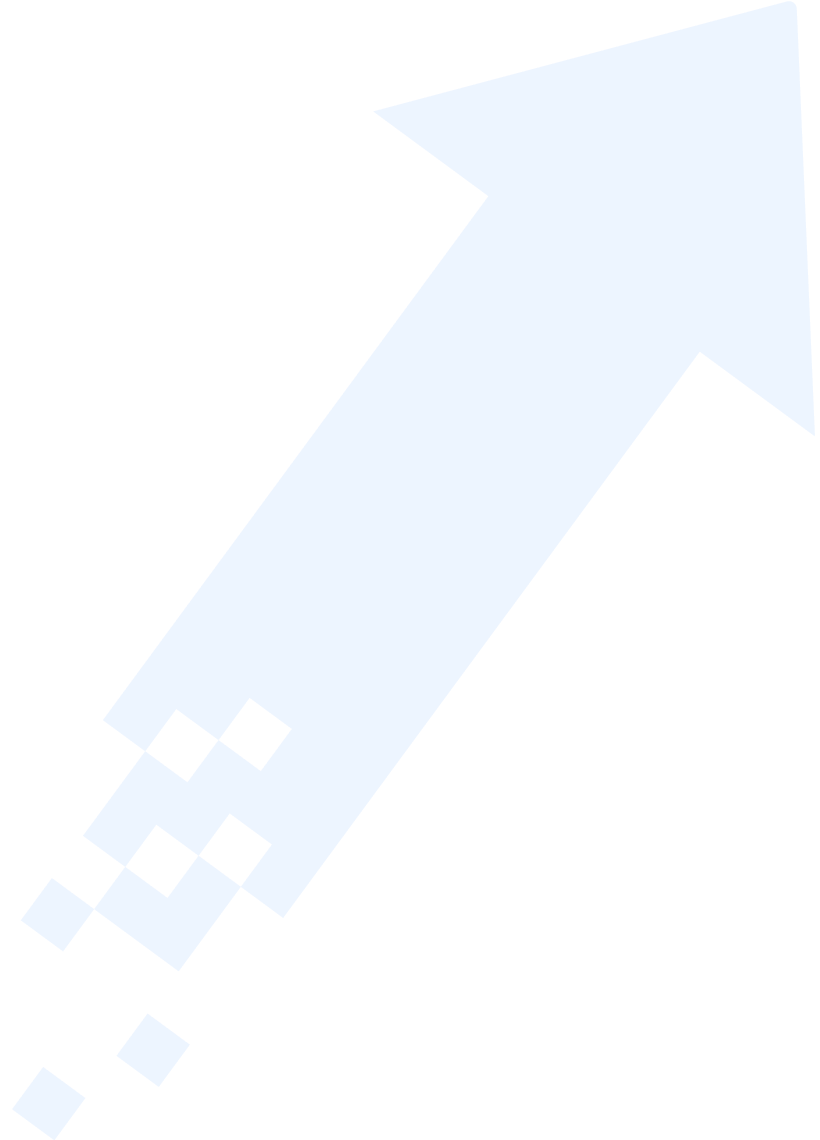
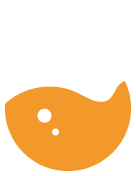
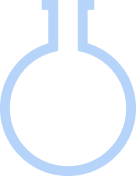
Industry Trend
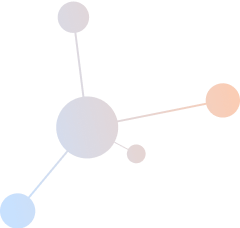

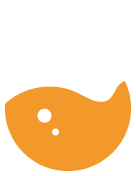
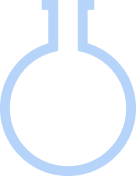
Why Us & Case Sharing
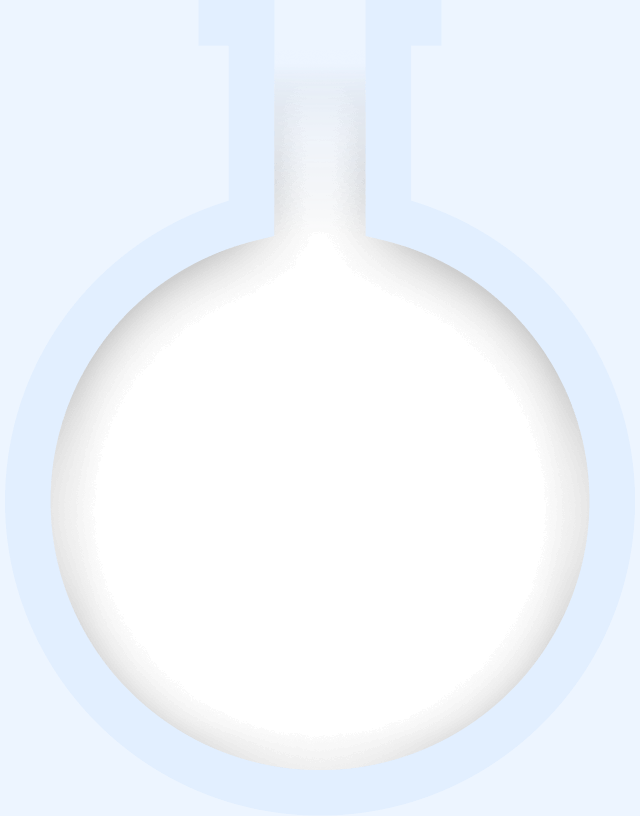
A dissolving pulp mill faced the high deposit (slag) built up in the recovery boiler, which significantly reduced heat transfer efficiency. This resulted in a short water wash cycle and increased washing frequency, impacting the overall pulp production throughput.
With detailed inspection and analysis by our pulp mill team, a patented technology, AmiSperse AP 8211, was applied and optimized the number & locations of dosing points (injectors)
- Reduced water wash frequency from 5 to 2 times per year
- Increased water wash cycle from 60 to 175 days
- Reduced carbon footprint through:
- Improved efficiency of soot blowers and reduced steam consumption
|
With AmiSperse AP 8211 application, the recovery boiler reached a new record for continuous running without production stoppage & water wash for 372 days.
For further details, please ask our expert below
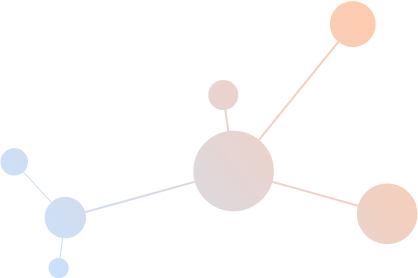
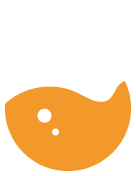
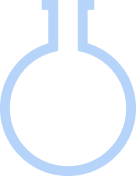
Ask Our Experts
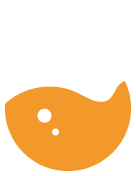
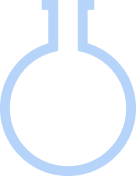