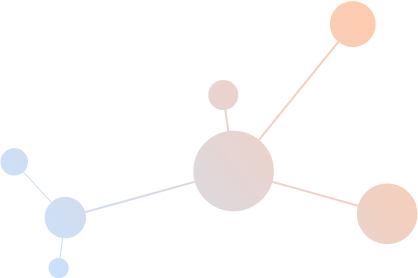
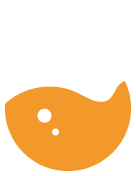
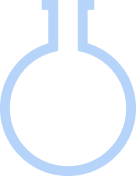
How It Helps
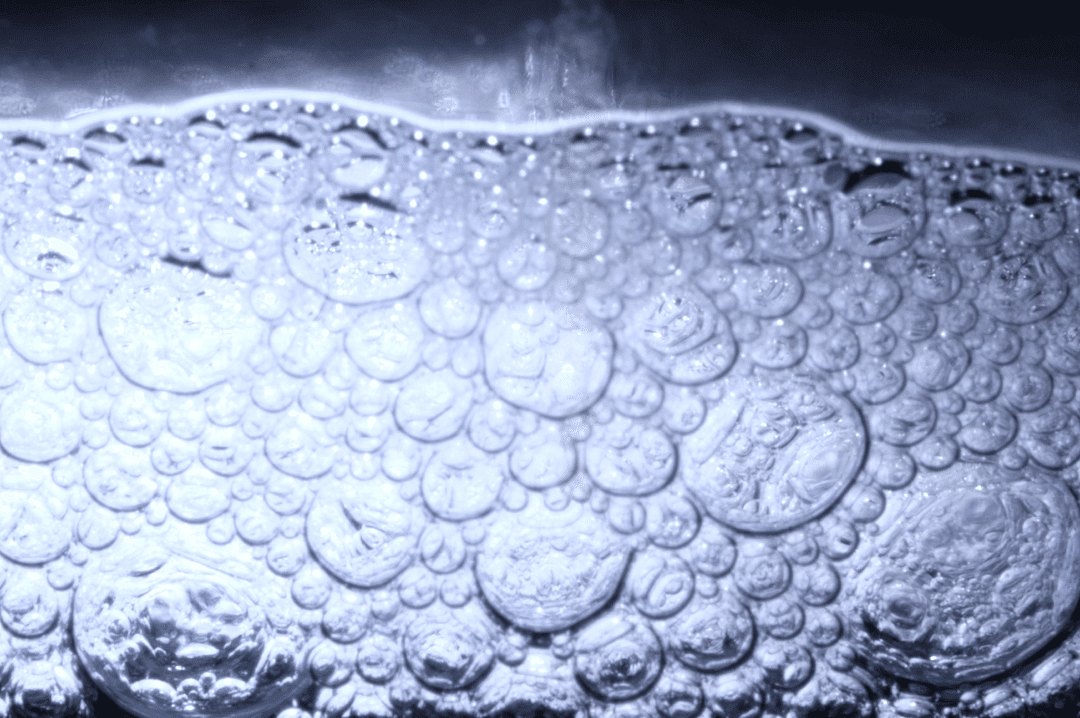
Pulp and paper-making systems are foam-generating systems and to achieve quality, production and cost goals, surface foam and entrained air must be controlled. In the pulp mill, Silicon defoamers and wash aids are used to increase the capacity of the brown stock system by improving drainage. Surfactant and Water based defoamers are preferred in the bleaching section. Improving washing efficiency with defoamers translates into cleaner pulp, generating savings from lower evaporator costs, reduced soda losses, and reduced bleaching chemical demand.
In the paper-making process, some of the typical challenges associated with surface foam and entrained air in stock (measured by EGT) are higher deposits on the air-water interphase area and causing sheet breaks, reduced drainage due to higher % of the air in stock, Sheet defects and poor sheet quality and Housekeeping/Safety issue. Surfactants, Water based (Fatty alcohols) defoamers are prevalent in the Paper mill wet end area.
Coating (both in Size press and pigment coating) require defoamers as the thin films are laid on the sheet and small bubble (foam) create sheet defects, impacting the penetration through the sheet and printing defects. Surfactants, oil-based and fatty alcohol-based defoamers are often used in these sections, depending on the type of additives and different formulation
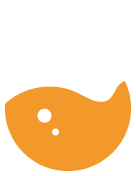
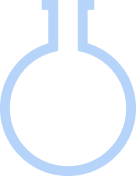
Application Areas
Effective control of foam and entrained air in all types of pulp & paper produced can provide the mill with additional capacity, higher quality pulp and paper, and cleaner systems. Amazon's AmiDefoam programs effectively control foams in pulp mills (Brown Stock Washing), Bleaching, Pulp Dryers, Wet end of Paper, Board and tissue machines, size press, coating, effluent treatment plant and many other locations in the pulp and paper processes.
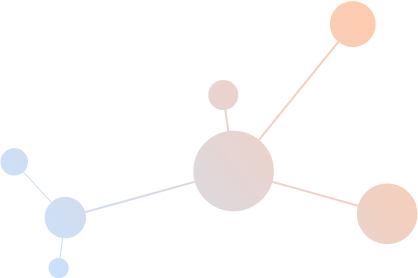
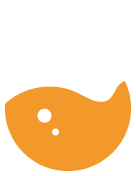
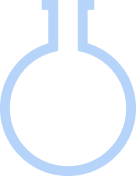
Ask Our Experts
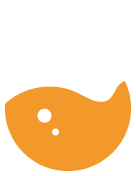
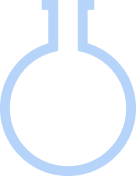