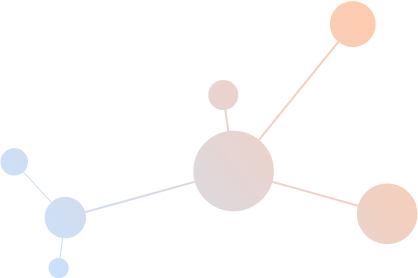
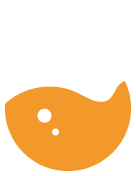
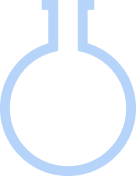
How It Helps
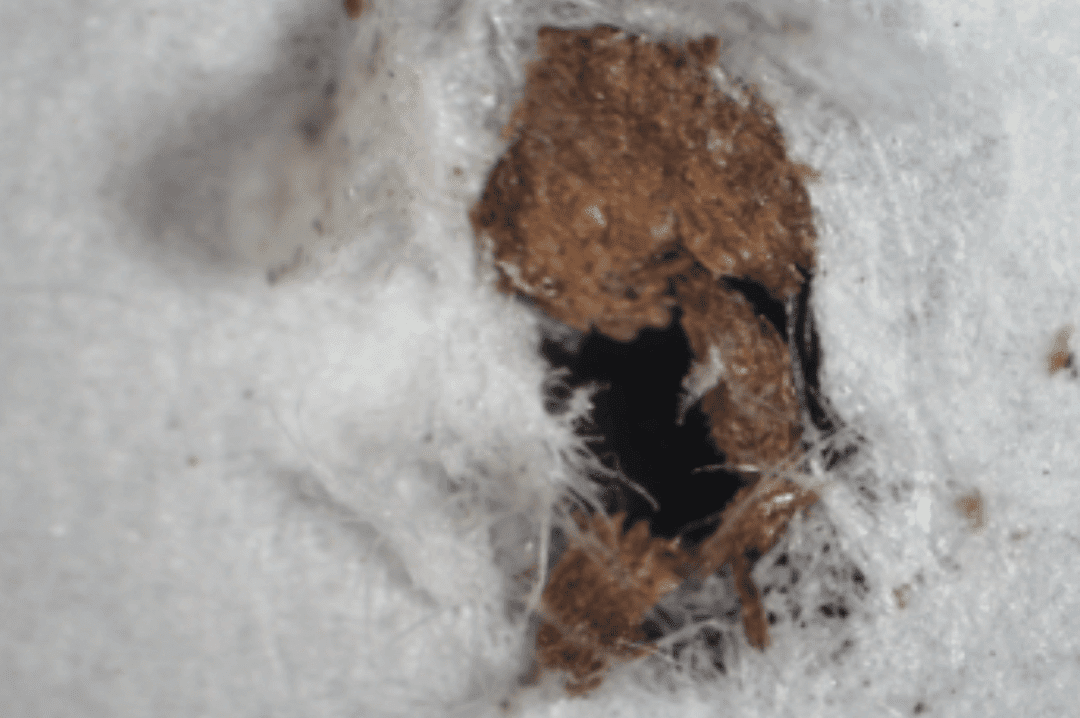
Pitch deposits (on their own or agglomerated with other inorganics) can appear anywhere in the Pulp & Paper making process. It could occur in places ranging from the pulp washing plant, screening, bleaching, stock preparation, wet end of pulp dryer or a paper machine to the final product, i.e. pulp or paper. The wood's resin interferes with other additives and causes sheet defects ( Dirt of blue deposits), breaks, etc. The shortage of fibrous raw materials, mixing of two different raw materials and limitations on debarking increase the need for pitch control. A combination of different chemistries (Surfactant, Dispersants encapsulations etc) provides the following benefits:
- Effective removal of Resin/Pitch from fibre in the early stages of production.
- Control of pitch deposition in the entire fibre line.
- Minimization of dirt and Extractive content in pulp and paper sheets.
Using alternative raw materials like Acacia and younger wood increases the overall resin content in the pulp (DCM Extractive in most paper-grade pulp range from 0.15 to 0.35%). The solvent used for extracting the resins defines its name as DCM extractive or Benzene Acetone Extractive. Surfactant and dispersant based chemistries are used in the pulp mill process (Digester, Washing, ODL and bleaching) to reduce the overall resin content in the pulp.
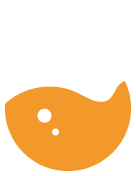
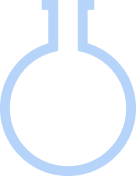
Application Areas
Various products like Digester additives and Pitch/Resin control agents are typically used at multiple feed points in the pulp mill process: digesters, brown stock washing process, oxygen delignification, bleaching process and pulp dryers. Encapsulation-based chemistries are typically used in pulp dryers and less complex open systems (Less degree of recirculation).
Localized treatments, such as wire passivation and felt conditioning, can be cost-effective alternatives for pitch problems in pulp dryers and paper machines.
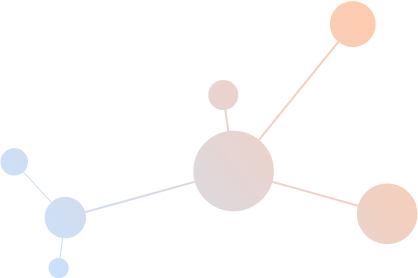
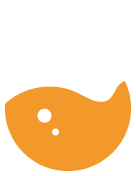
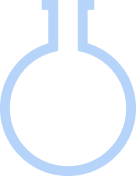
Ask Our Experts
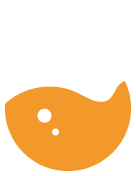
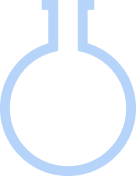